This website uses cookies so that we can provide you with the best user experience possible. Cookie information is stored in your browser and performs functions such as recognising you when you return to our website and helping our team to understand which sections of the website you find most interesting and useful.
How Unmanned Systems are Improved with Etched Components
The history of unmanned systems dates back further than most realize. Some of the earliest recordings include:
- 200 BC – Chinese used paper balloons equipped with oil lamps to fly over enemy territories to instill fear.
- 1783 AD – The first public demonstration of a hot-air balloon in Annonay, France.
- 1918 AD – An American aerial torpedo was flight tested.
As technology continues to advance and components continue to get smaller, unmanned systems can be found in the air as Unmanned Aerial Vehicles (UAVs), on the ground as Unmanned Ground Vehicles (UGVs), and in the water as Waterborne Unmanned Vehicles (WUVs). They are being used for different applications including:
- Patrol Security
- Disaster Response
- Environmental Monitoring
- Survey/Mapping
- Reconnaissance/Surveillance/Intelligence
- Imaging
Depending on the application, the overall design and parts within an unmanned system vary among aerial, control, and communication components.
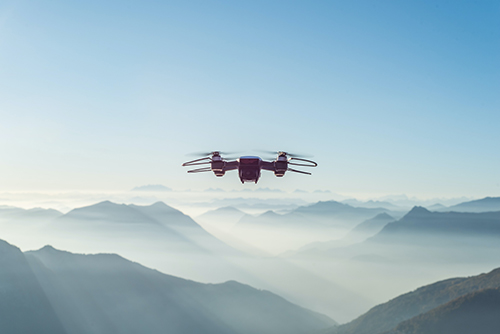
Photochemical Etching for UAV Components
Whether an unmanned system is in the air, on the ground, or in water, its design needs to be safe, reliable, and cost efficient while also featuring a certain aesthetic. Their overall construction needs to be lightweight and durable so they can easily maneuver and withstand various environmental challenges during operation.
Photochemical machining, or acid etching, is a manufacturing process that fabricates parts from different types of sheet metals ranging in thickness from 0.0005 inches (0.013 mm) up to 0.090 inches (2.286 mm).
Etching, regardless of simple or complex geometries, maintains the physical characteristics of the metal for unmanned system components. Commonly etched components include EMI and RFI shields, antennas, various sensor elements, electrical contacts, encoders, fuel cells, heat exchanger plates, semiconductors, and more.
UAV Diffusion Bonded Fuel Cell Plates
Hydrogen fuel cells are becoming quite popular among UAVs for several reasons, including:
- Increased flight distance and flight time.
- Increased productivity and higher energy density, providing a greater energy output to mass ratio.
- Quiet operation for stealth missions.
- Better endurance and less required maintenance compared to internal combustion engines.
Photochemical etching is a great fabrication process to produce burr- and stress-free plates with the internal intricacies need for the overall fuel cell block, without adding the cost as production quantities increase.
After each plate is etched, diffusion bonding can be used to internally join the plates together to create the fuel hydrogen fuel stack without affecting the parent properties of the metal. This process is great for plates thicker than 0.63 inches or for plates that require tight intricate channels within a larger plate.
Keeping Things Small and Lightweight
Reducing the weight of a design is essential to minimizing energy consumption, but the miniaturization of components is not an easy task. There is a lot to consider in terms of materials and fabrication processes. Some drone frames are made with titanium, aluminum, or carbon fiber-reinforced composites for lightweight and durability requirements.
On the inside, various material components are assembled for the motors, electronic speed controllers, control boards, radio transmitters, battery components, and electronics. Other options, depending on the purpose of the drone, include propellers, landing gear, and camera components.
Many manufacturing processes can alter the inherent characteristics of a metal negatively affecting a design’s overall quality and performance which could be catastrophic in industries such as aerospace and defense.
Processes like CNC machining or welding can deform the metal by creating burrs or heat-affected zones or can change the metal grain structure. If the burrs are not removed, unwanted friction and heat can occur, causing the part to fail and requiring more frequent replacements.
Heat-affected zones are weakened areas that change the structural integrity of the metal. Burrs and heat-affected zones negatively affect the tight tolerance requirements for intricate, complex geometries.
Chemical etching simultaneously etches the part without applying heat, inducing stress, or creating burrs, maintaining the purity of the metal while maintaining tight tolerances required in high-reliability applications.
Acid-Etched Metals Found in Unmanned Systems
A variety of metals used for the construction of parts found in unmanned systems can be photochemically etched, including:
These metals are used for their high strength, durability, corrosion resistance, and thermal and electrical conductivity properties.
The photochemical machining process uses a strong caustic chemical and a photoresist to define selective material removal. It etches unprotected areas of the metal surface to create intricate designs with complex geometries.
Regardless of the metal selected, chemical etching offers several advantages compared to other fabrication processes and answers the demand for low-cost, burr-free parts. Intricate parts that are impractical to machine, because of the hardness or brittleness of the work material, can be produced with ease by chemical etching.
Additional Assets of Chemical Etching for Unmanned Systems
The challenges that can arise when fabricating complex parts using traditional metal machining methods can be solved with chemical etching. Other advantages the process provides, include:
- Fabrication of magnetically soft materials while retaining optimum permeability.
- Fabrication of extremely brittle metals without fracturing.
- Digital tooling for rapid prototyping and high production volume orders without additional costs due to machine downtime or hard tooling changes.
- Quick turnarounds and lead times with reduced costs and waste.
With the ability to etch the most intricate design from the most difficult metals without increasing costs or lead times, photochemical etching is a great process to consider for unmanned systems components.