This website uses cookies so that we can provide you with the best user experience possible. Cookie information is stored in your browser and performs functions such as recognising you when you return to our website and helping our team to understand which sections of the website you find most interesting and useful.
Precision Metal Forming
Fotofab provides a full range of metal bending and forming services on a rapid delivery basis. We manufacture all our own tooling in-house so that we can control quality and lead times. Our system of forming uses simple tooling which can be built quickly and inexpensively.
Rather than making costly progressive dies, tooling is broken up into multiple stations. At each stage, an individual operation is performed such as a single bend. These stations can be made in parallel, saving time.
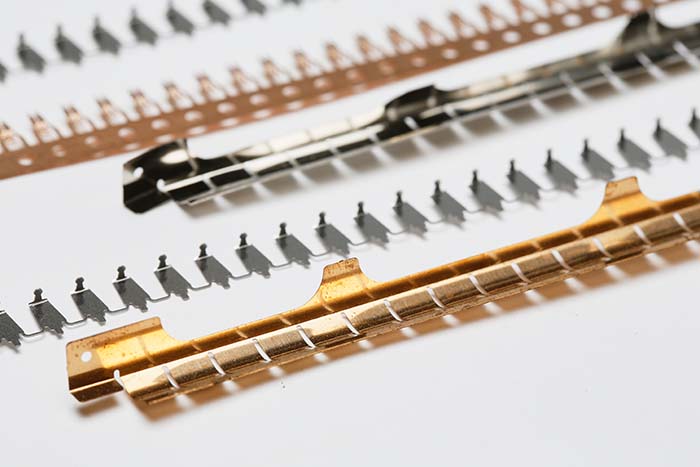
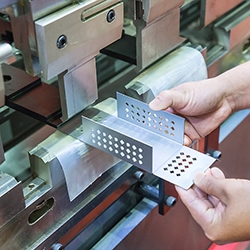
Precision Metal Forming Capabilities
Fotofab works with material thicknesses from 0.0001” to 0.125” (0.0025 to 3.175 mm), depending on the features required. Like the chemical etching process, our standard lead time is one week. Expedited lead times are available in as little as one day.
Whether you have a fully formed dimensional drawing or need engineering support, our engineering team can work with you to help design the blanks and tooling required. We are experts in knowing how to etch and bend the parts to their final shape and want to provide feature-complete parts so you can begin using them instantly.
Advantages of Precision Metal Forming Process
- Speed: Parts can be formed in as little as one day
- Precision: Tolerances can be held as tight as +/- 0.001” (0.025mm)
- Cost: Tooling cost is minimal
- Flexibility: Multi-station tooling allows geometries not otherwise achievable with progressive dies
- Reliability: All parts are made to Fotofab’s exacting quality and craftsmanship standards
- Growth: Short prototype runs can smoothly transition to mass production runs
In-House Tooling that Saves Time and Costs
Fotofab stocks pre-built tools for dimpling and simple 90-degree bends, so we can save time on your next project. Precision metal forming methods available:
- Kick Presses, 30+ on-site
- Hydraulic Presses, including a deep draw press that allows the manufacturing of drawn cans
- 4-Slide Machines, which can be used for stamping and forming
- Hand Forming
Forming Equipment
Kick Presses
Fotofab most often uses kick presses for forming. They are quick to set up and ideal for low-cost tooling. Even when built quickly, our results are precise and repeatable. Unlike other methods used by many prototype shops, our approach does not rely on the manual work of operators, but rather, robust tooling. This ensures the same result every time and is ideal for rapid prototype parts.
Hydraulic Presses
Hydraulic presses are ideal for thicker metals or parts requiring additional force for bending, drawing, or coining. These presses can be used for what Fotofab calls a one-shot tool. Unlike stage tooling, which requires a separate operation for each bend, a one-shot tool performs all operations in a single strike. These tools cost more than stage tooling but can pay for themselves at a lower part cost with adequate volume. The break-even quantity will vary based on the geometry of the part.
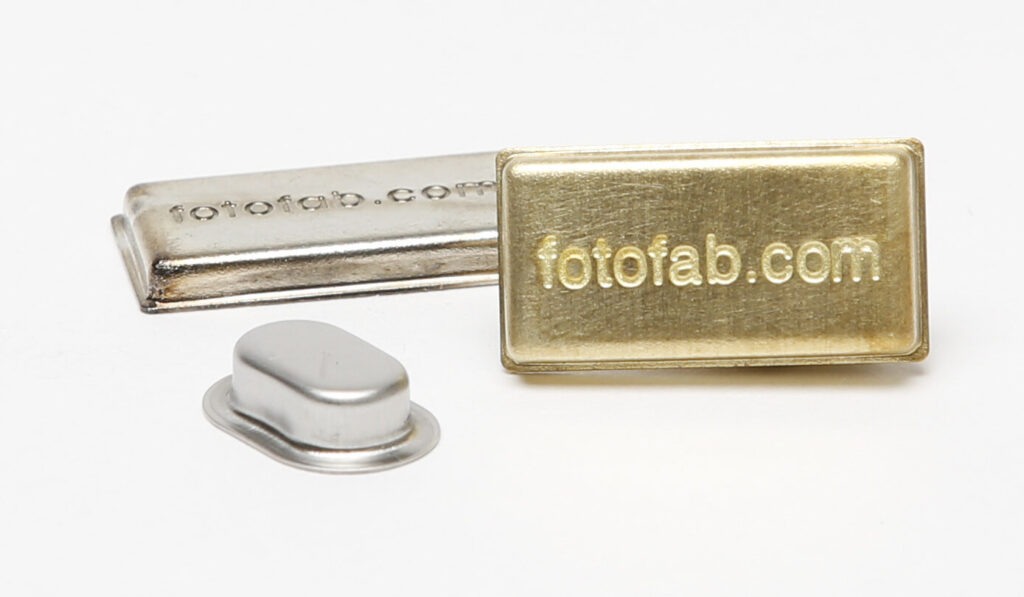
Drawing Cans
Fotofab produces drawn cans in rapid prototype and production quantities. A drawn can is a seamless, 5-sided box with rounded corners, made by stretching or “drawing” the middle of a rectangular blank. They can be made from material 0.010″ to 0.040” thick with a draw radius of 2.5x thickness and finished with or without a lip along the bottom. They can be very inexpensive and are also ideal for hermetic applications.
4-Slide Machines
4-Slide Stamping is suitable for smaller parts (0.002-0.32″ thickness, and typically narrower than 2″) with a less complex feature geometry. The machine is a horizontal press with 4 moving tools that strike the metal part from different directions. By working on 4 axes it is able to be very versatile and usually less expensive to tool than a progressive die.
This is most commonly used for contacts, springs, and small connectors made in a wide variety of metals. Our high-quality standards and craftsmanship remain the same whether the job is a short-run prototype or transitioned to a mass production run.
Hand Forming
For the quickest and least expensive option, Fotofab recommends hand forming. Hand forming is ideal for parts at least 0.008” thick (0.2 mm) with 90° bends and does not require tooling. To facilitate this, we half-etch a channel into the blank which serves as the inside of the bend and ensures an easy and accurate bend.
4-Slide Stamping
The features of a 4-slide stamping machine combine a unique forming operation that reduces cost, speeds up production, and delivers a better end product, even those with complex designs.
Available Metals
Explore Metals We Chemically Etch
Here at Fotofab, we provide photochemical machining (chemical etching, acid etching) services for a wide range of metals and alloys.
Fotofab is committed to quality.




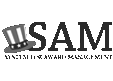
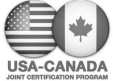